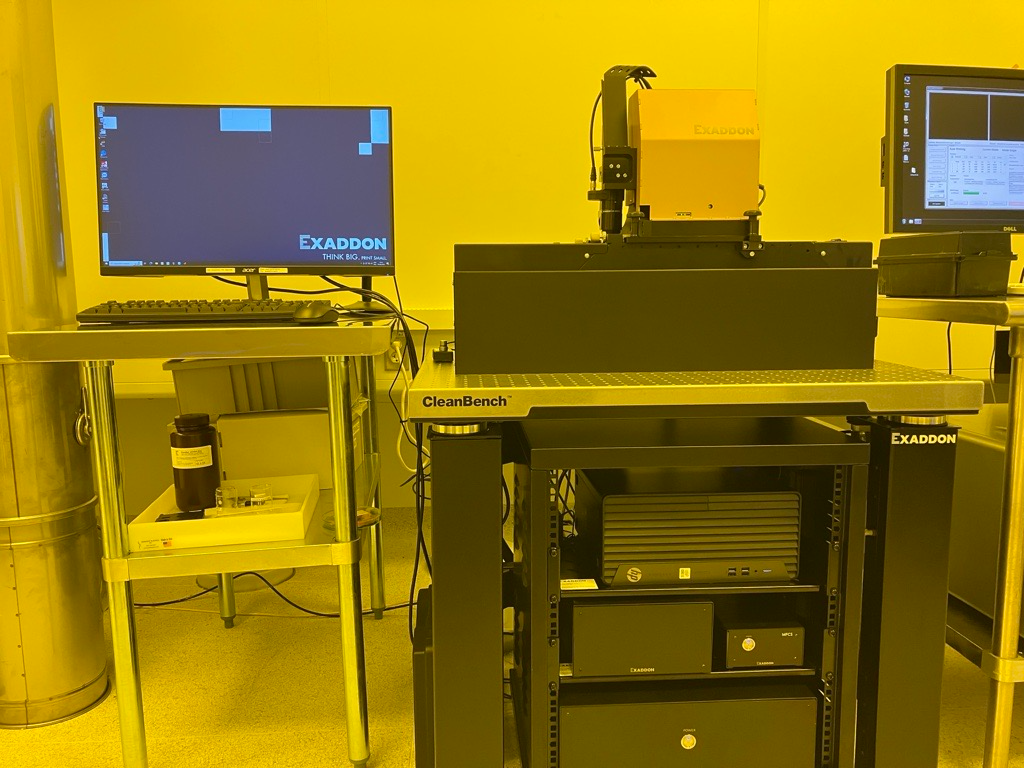
Exaddon CERES μAM
The Exaddon CERES μAM system prints microscale metal objects by electrodeposition. The system is optimized for printing free-standing microscale structures such as pillars, needles, coils, and lattices on existing surfaces, such as ICs or wafers.
Printing occurs at room temperature, and no post-processing is necessary. This system can print Gold, Copper, and Nickel. The printable size range is 1 μm – 1 mm, resolution < 1 μm, and structures can be located on print surfaces with <1 μm accuracy. This makes it ideal for applications in brain-machine interfaces, semiconductor surface modification, Photonics, Drug Delivery, and HF communication components.
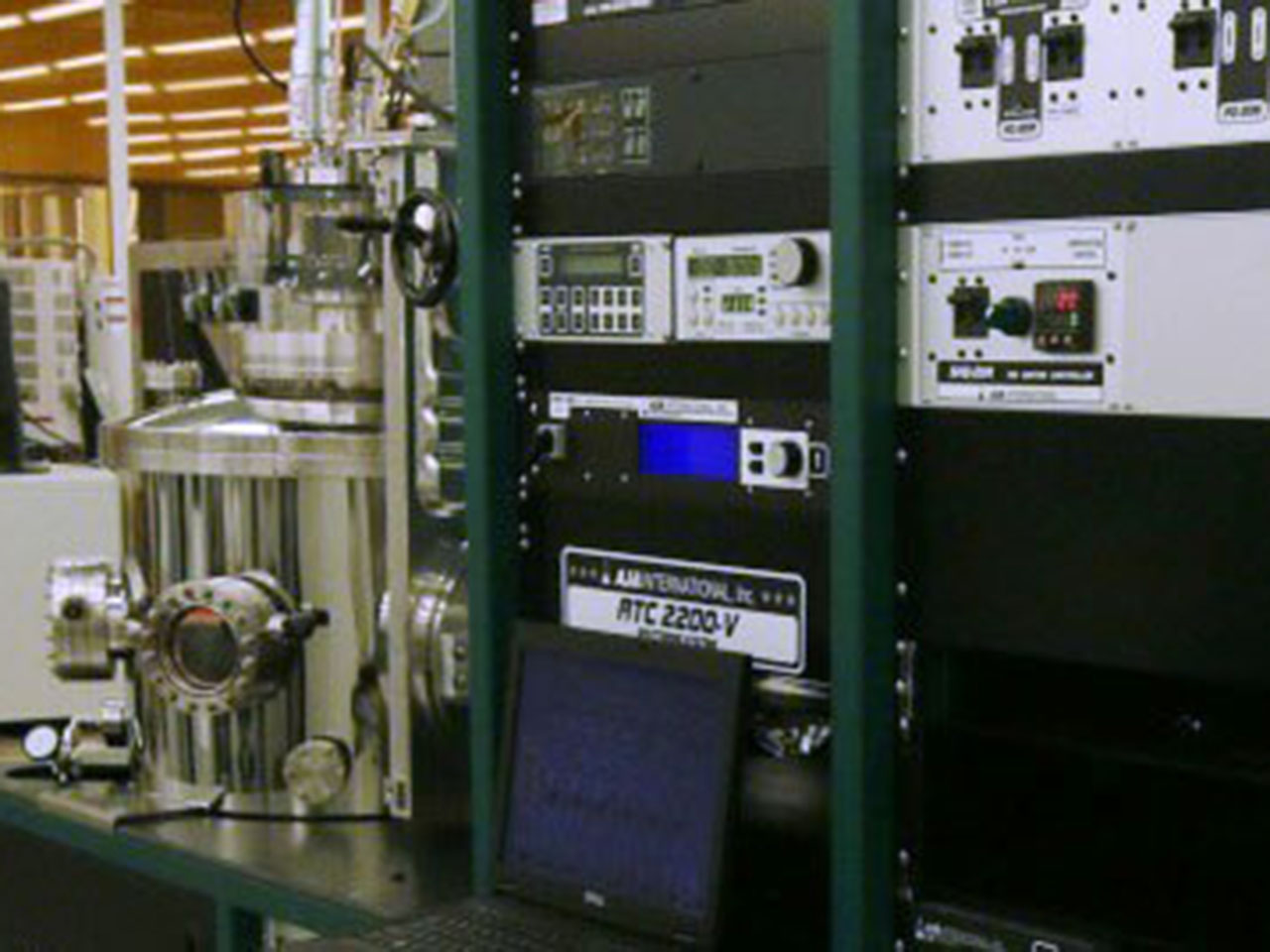
AJA Nitride Multisource Sputtering System
The Georgia Tech AJA Nitride Multisource Sputtering System deposits thin metal and nitride films in argon and nitrogen-enriched low vacuum. The AJA Sputterer has 4 magnetron sputtering guns, 2 DC power sources, 3 RF power sources, and a heater that can reach up to 800°C. It also has the capability of pulse dc. RF Bias is also available up to 50W. It can process wafers up to 4" -Deposition Processes: Aluminum, Aluminum Nitride, Titanium, Titanium Nitride, W, Mo, Ta, and Tantalum Nitride.
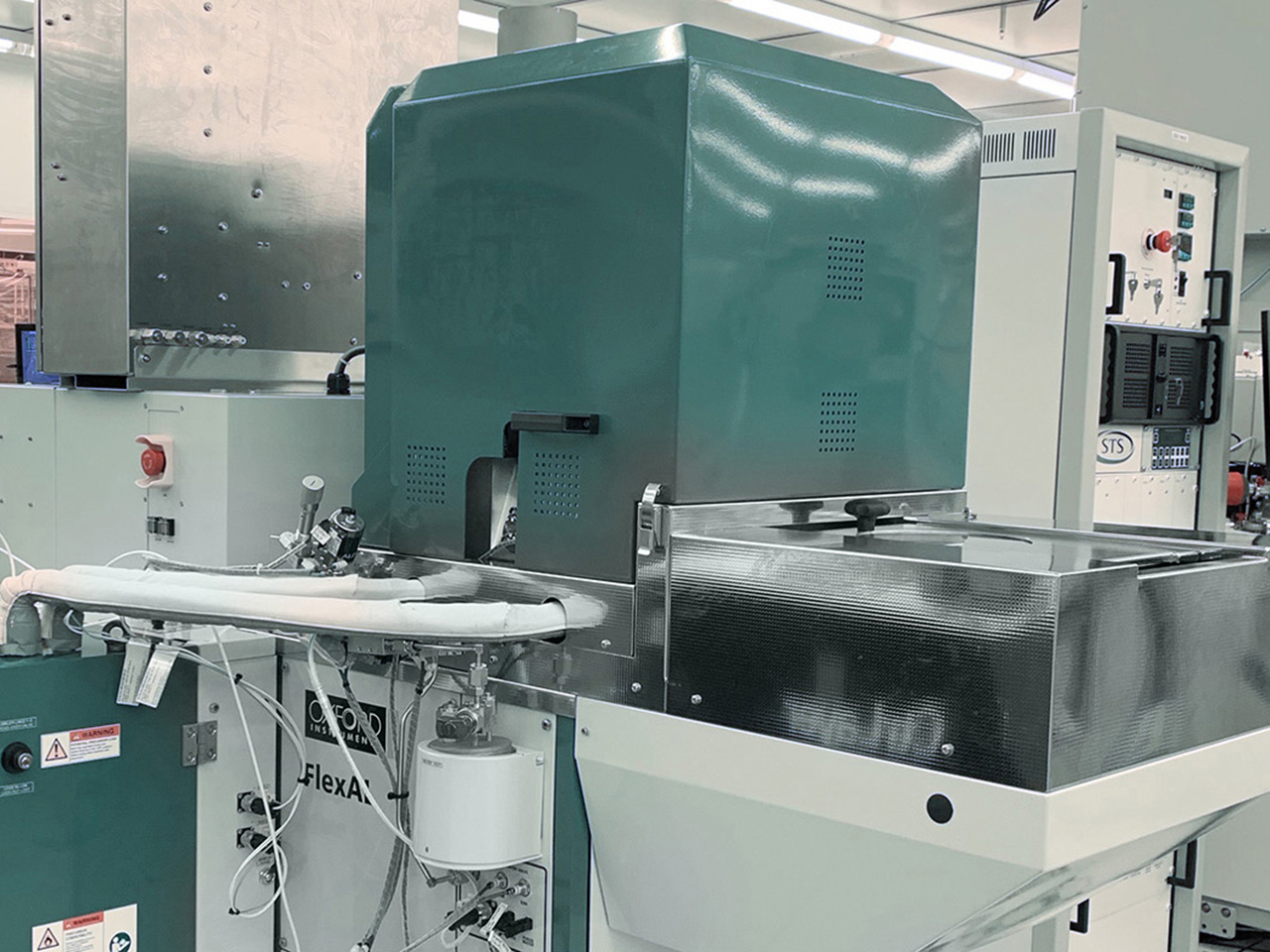
FlexAL Atomic Layer Deposition System
The FlexAL atomic layer deposition (ALD) system offers a broad range of optimized high-quality plasma ALD and thermal ALD processes with maximum flexibility in precursors, processes gases, and hardware configuration within a single process chamber.
Features include:
- Remote plasma for low damage plasma ALD combined with thermal ALD in one deposition chamber
- RF biased electrode option available for control of film properties
- Industry-standard cassette to cassette handling for higher throughput
- Maximum flexibility in the choice of precursors, process gases, hardware features and options
- Optimized to maintain low-damage, high-quality substrates
- Removable liners allow for easy chamber maintenance
- Low temperature to enable high-quality deposition on temperature-sensitive surfaces
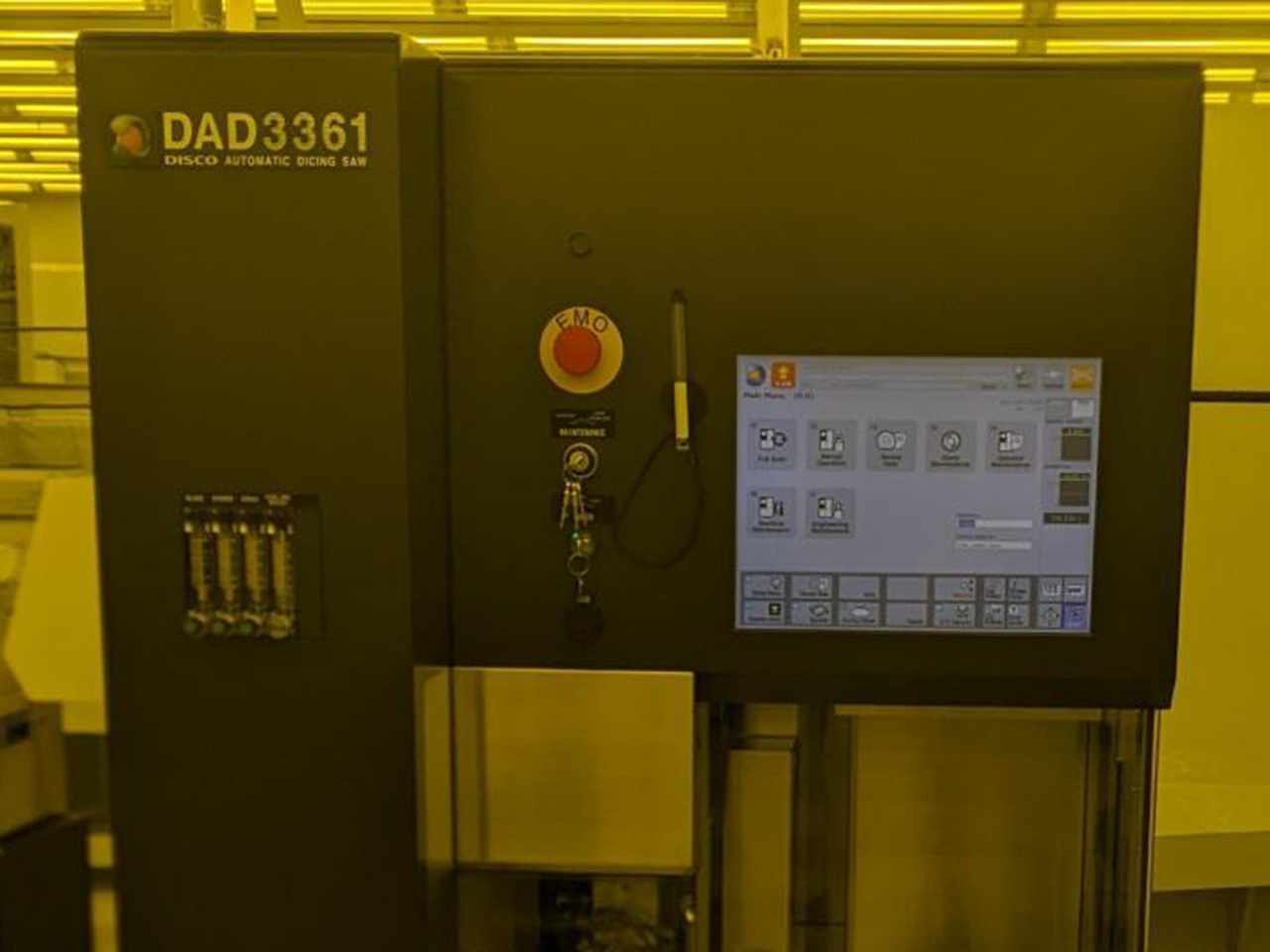
Disco Automatic Dicing Saw
The Disco Automatic Dicing Saw (DAD 3361) is an automated dicing saw that can handle 12-inch wafers and smaller substrates. The common blades are 80um thick and can cut glass and silicon substrates up to about 1mm thickness. For FR4, sapphire and other materials, special purpose blades can be used. The DAD3361 is commonly used to cut silicon wafers, but can also handle products of a variety of sizes and materials, such as large package substrates, electronic parts including SAW filters, and more. It has a wide selection of options available to improve processing quality to reduce running costs and improve its ability to process hard-to-cut materials. Alternative uses of the system can include the creation of trenches or scribing lines on substrates to aid in subsequent separation of small dies. The system also incorporates a semiautomatic and automatic alignment system to allow researchers at various levels of training successful use of the system. Substrates to be cut on the system are affixed to the dicing frame and chuck table with a UV release tape to allow for a strong adhesion during dicing and easier removal of diced substrates after the dicing process.
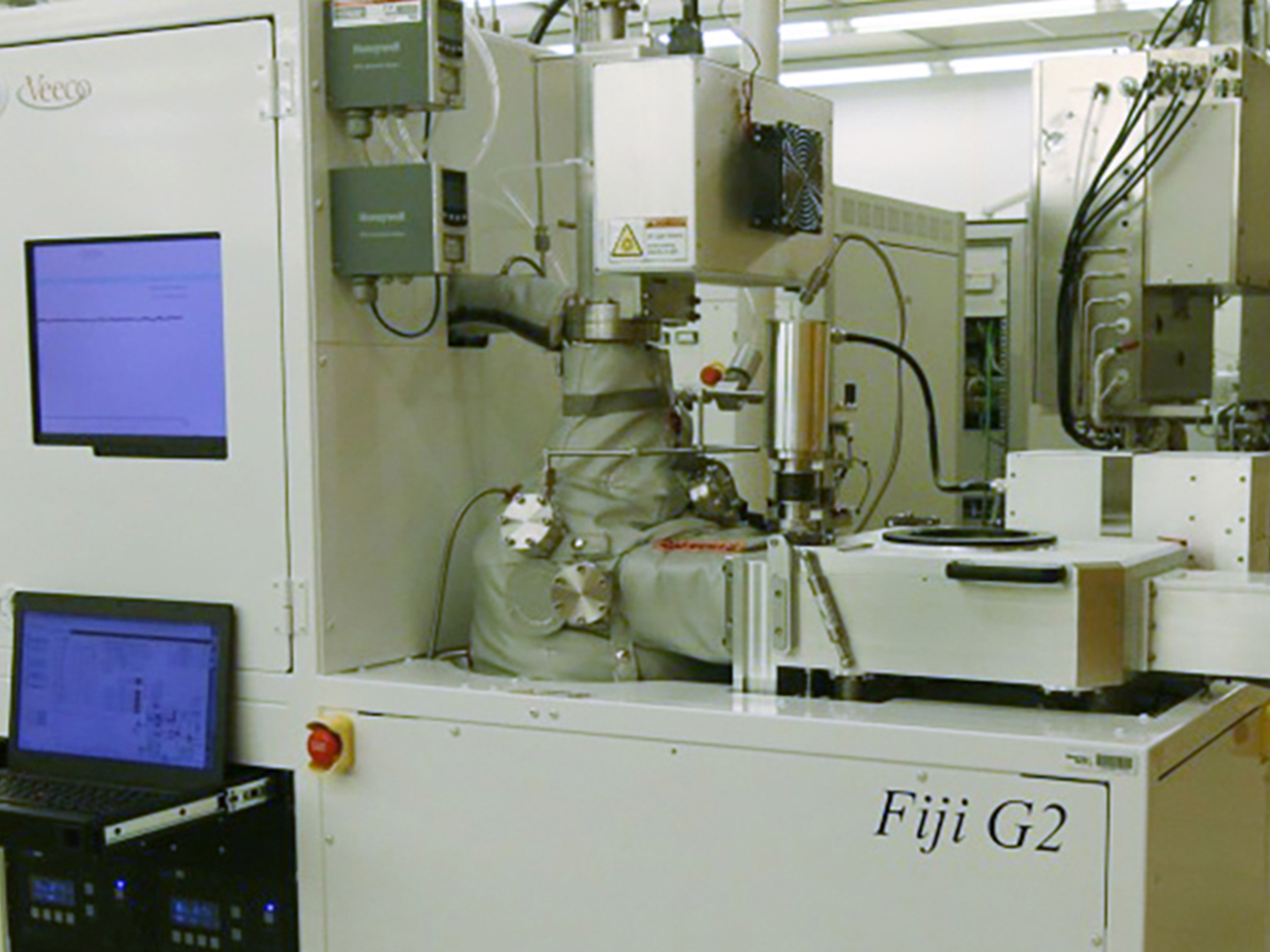
Veeco Fiji G2 Atomic Layer Deposition System
The Veeco Fiji G2 Atomic Layer Deposition (ALD) System is a modular, high-vacuum ALD system that can accommodate a wide range of deposition modes using a flexible architecture and multiple configurations of precursors and plasma gases. The Fiji G2 is a next-generation ALD system capable of performing thermal and plasma-enhanced deposition. It has advanced features including a proprietary chamber turbo pumping system, fast process time, and improved plasma design.
The Veeco Fiji G2 ALD System has a 200 mm (8”) chuck with fully automatic loading and unloading function. The process temperature can be up to 500°C, and plasma power up to 300 W. The layer thickness can be controlled to angstrom resolution, and uniformity of layer thickness is within 1% across the deposition area. It can generate high quality oxide and nitride films for semiconductor manufacturing, MEMS, solar cells, etc.